Nach langer Zeit mal ein Update. Ich habe leider super viel um die Ohren und das Wetter spielt mir bei dem Projekt auch nicht in die Karten. In dem Treibhaus sind aktuell immer zwischen 30-40°C. Da sind mehr als 3-4 Stunden leider echt nicht machbar. Aber wir kommen langsam voran:
Ich habe die Versteifungsrohre am Heckspiegel bündig abgetrennt. Anschließend habe ich den Heckspiegel vorgespannt und fürs Schweissen vorbereitet.
Anschließend habe ich das ganze mit einem Propanbrenner vorgewärmt um den Wärmeverzug zu mindern und einen saubereren Schweissprozess zu haben. Hierbei wäre ein Acetylen/Sauerstoff Brenner besser geeignet. Habe ich leider aber erst jetzt verfügbar.
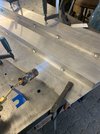
Und jetzt kommt der Fail:
Ich habe leider richtig starken Verzug durch das Schweißen bekommen. Ich war leider der Meinung, dass man es nur fest genug vorspannen muss und dann keinen Verzug hat. Scheinbar ist genau das Gegenteilige der Fall. Ich habe jetzt eine Durchbiegung im Heckspiegel vom etwa 2-3mm. Er ist also etwas verbogen. Es ist echt absolut Irre was dabei für Kräfte wirken. Das ist 8mm hochfestes Aluminium.
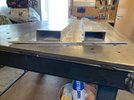
Man kann hier auf der Rückseite genau erkennen wo geschweißt wurde. Und genau an diesen "Linien" hat sich das Bauteil gekrümmt. Ich kann jetzt daran nichts mehr machen. Es sollte weder funktionell noch sicherheitstechnisch ein Problem darstellen. Nur mein Ego ist stark angekratzt
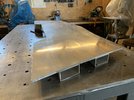
Weiter ging es dann damit die provisorischen Schraubzwingen am Baugestell zu entfernen und durch Schrauben zu ersetzen. Die entstandenen Löcher kann ich am Ende einfach wieder dicht Schweißen. Das ist kein Problem.
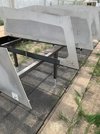
Nun ging es daran den Heckspiegel zu montieren. Ich habe dazu ein paar Vierkantrohre als Montagehilfen angeschweißt. Diese sind genau so ausgerichtet, dass der Heckspiegel am Ende eine Neigung von 14° haben wird. So wie es der Bauplan vorsieht.
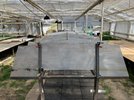
Anschließend habe ich den Kiel eingesetzt. Dieser muss noch etwas angepasst werden wo er auf den Heckspiegel trifft.
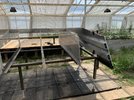
Ich konnte es mir dann nicht nehmen lassen den ersten Stringer probesitzen zu lassen. Passt grundsätzlich schonmal sehr gut. Nur die tiefe muss ich an jedem Spanten noch so anpassen, dass Stringer und Spant bündig sind. Sonst würde ich einen Hohlraum unter der Aussenhaut haben. Das ist dann einer der vielen folgenden Schritte.
Soweit erstmal von mir. Das sieht alles bestimmt nach gar nicht so viel Arbeit aus, aber alleine der Heckspiegel hat mich mit dem Wärmeverzug fast zur Weißglut getrieben. Ich habe aber auch gemerkt, dass ich manchmal "fünf gerade sein lassen" muss. Es ist ja immernoch ein Hobbyprojekt und kein professioneller Bootsbau. Fällt mir leider nicht einfach
In den nächsten Schritten werde ich dann das Schweissen am "Boot" beginnen. Heckspiegel und Kiel werden geheftet und dann richte ich jeden Spant nacheinander genau aus und hefte diese ebenso an. Danach kann ich die Stringer einsetzen und anpassen und ebenfalls heften. Stück für Stück
